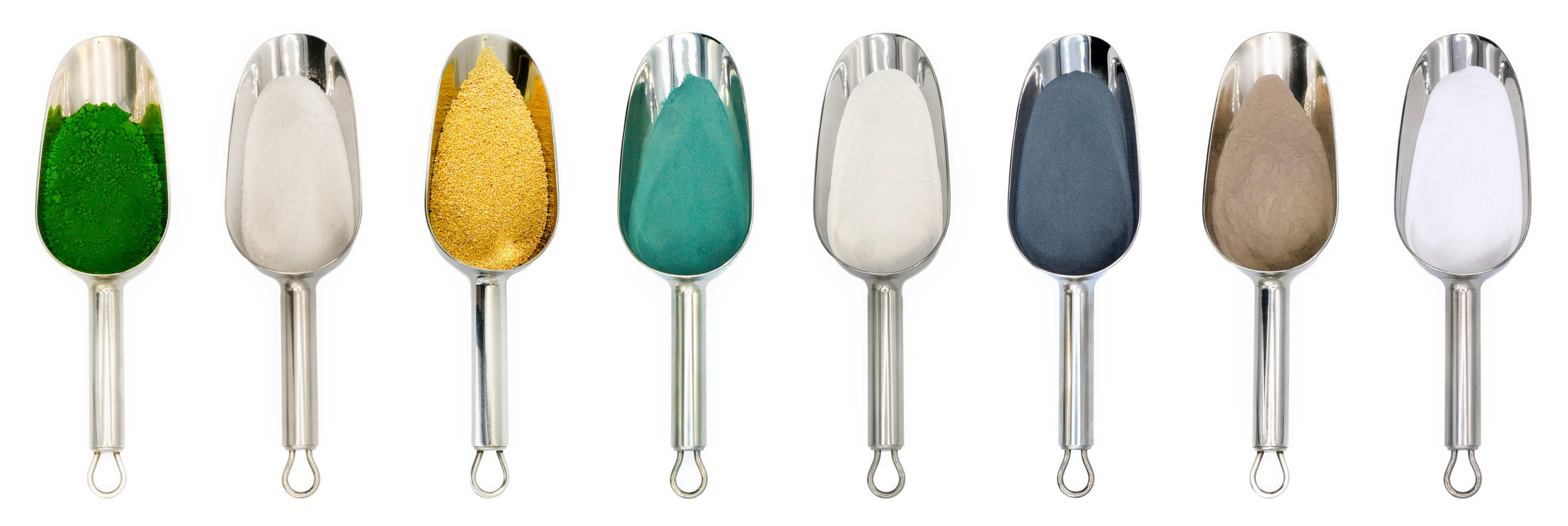
Technical Ceramics
The material field of technical ceramics opens new possibilities of productivity for the progressively growing industry. These possibilities arise from the extension of the operating conditions and lifetime of tools, plant components and products.
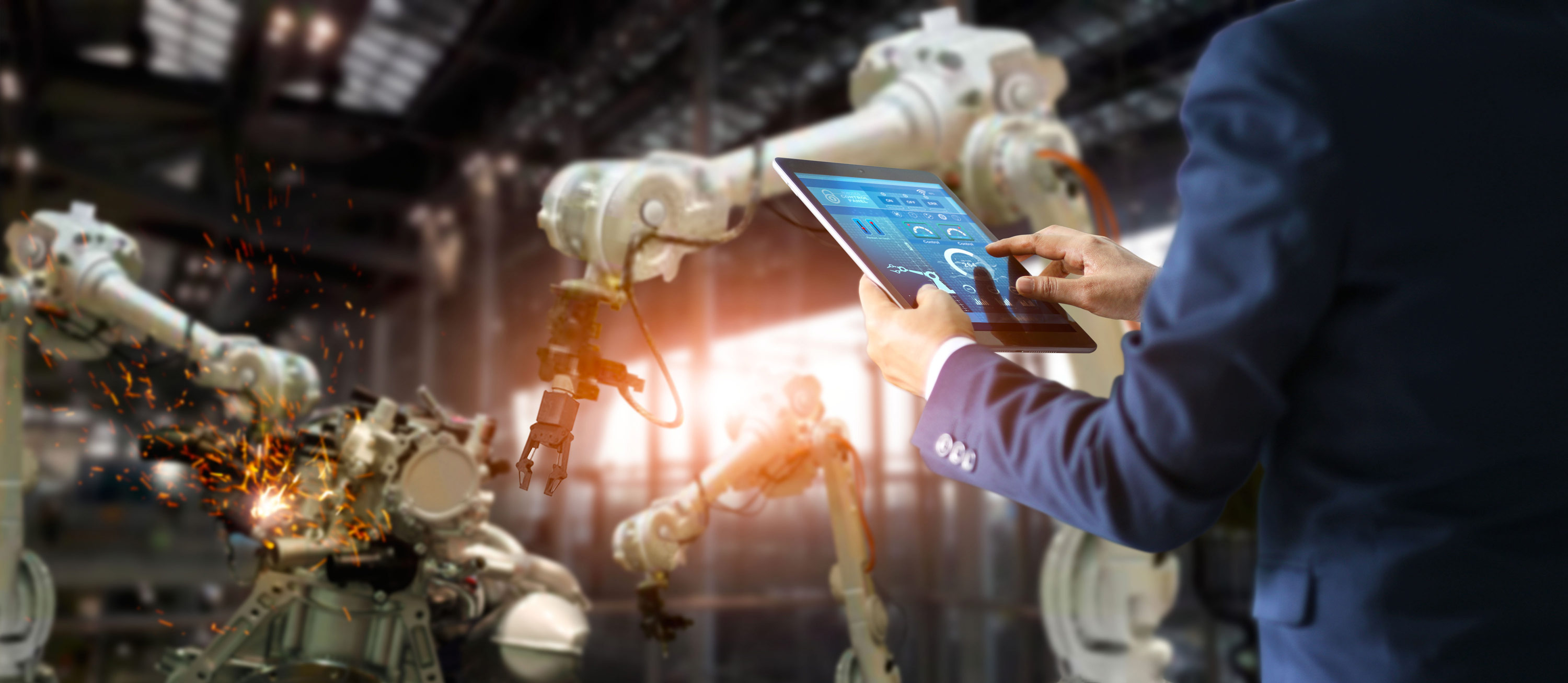
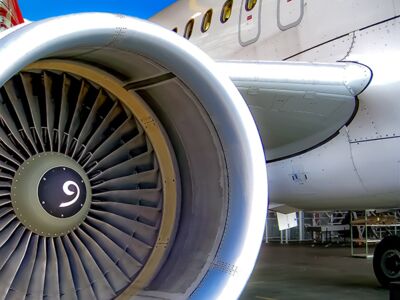
As technical ceramics, non-metallic, inorganic and (partly) crystalline materials are referred to, which are applied in industry due to their specific properties[RIE08]. In contrast to classical ceramics, no naturally occurring minerals but chemically prepared or synthetically produced starting materials are used, whose composition can be precisely adjusted, especially for high-performance ceramics[GAU01]. Thus, the properties can be specifically and reproducibly adapted to the desired industrial application.
Ceramics are generally characterized by high hardness and wear resistance, good corrosion resistance and outstanding thermal properties, in particular a high melting point and low thermal expansion[HEI10] and can therefore be used in fields in which conventional materials would fail.
For example, in high-temperature engineering refractory linings and burner nozzles made of ceramic. The high wear resistance of technical ceramics allows their use as sliding and sealing elements with long service life [KOL18].

Thanks to their wide range of electrical properties, technical ceramics are just as essential for the electrical and electronics industry. Among others, they are used as isolators, (semi) conductors, piezo elements and varistors[HEI10]. Due to their biocompatibility and chemical resistance, ceramics are also indispensable in medical technology, especially implantology [KOL18].
Based on their composition, ceramics can be subdivided into three main groups:
- Silicate ceramics
- Oxide ceramics
- Non-oxide ceramics
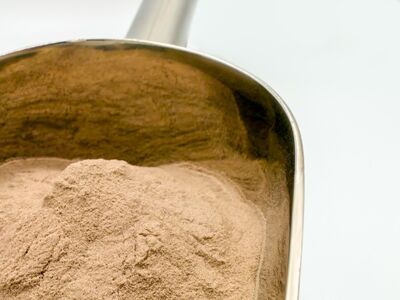
Silicate ceramics were the first ceramics used for technical applications. They are still mostly produced with naturally occurring minerals and are usually composed of a high proportion of silicate glass phase [KOL18]. Due to the high availability of the raw materials and their relatively low sintering temperatures, silicate ceramics are among the cheapest representatives of technical ceramics. They are mainly used as insulators in high and low voltage engineering.
The oxide ceramics include essentially single-phase metal oxides such as aluminum(Al2O3),magnesia(MgO) and zirconia (ZrO2). They are characterized by significantly higher melting points than silicate ceramics, high hardness and a fine microstructure with very small particle size[KOL18].
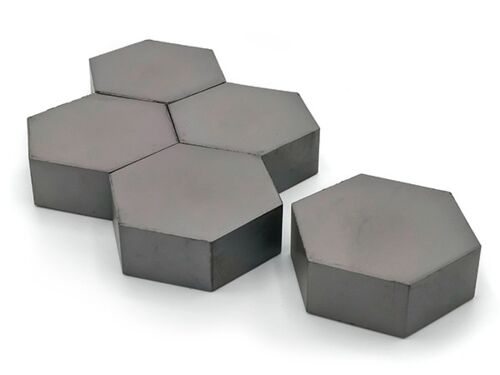
The most important representatives of non-oxide ceramics are carbides and nitrides, but also borides, silicides and fluorides, as well as modifications of carbon (diamond, graphite, etc.). The extremely wide range of elements and chemical bonding conditions causes the heterogeneity of this group. Common features are very high hardness (HV ≥ 2000N/mm-2) and a high melting point (Tm ≥ 2400 °C, apart from Tm (Si3N4) = 1900 °C)[HEI10].
The processing of these high-performance ceramics requires extremely fine powders and very high sintering temperatures, usually in an oxygen-free atmosphere[KOL18]. This leads to higher costs for the processing and consequently for the material itself.